A programmable rednet controller (PRC) is a specialized computing device designed to automate and monitor industrial processes and machinery within a distributed network. PRCs excel in applications that require reliable, real-time control and remote access capabilities.
PRCs offer numerous advantages, including enhanced productivity through automation, reduced downtime due to predictive maintenance, and improved energy efficiency. Their ability to integrate with diverse sensors and actuators enables comprehensive data acquisition and control, providing valuable insights for process optimization.
The adoption of PRCs has revolutionized industrial automation, facilitating the development of smart factories and Industry 4.0 initiatives. Their versatility and adaptability make them suitable for various sectors, including manufacturing, energy, and transportation.
Programmable Rednet Controller
Programmable rednet controllers (PRCs) hold immense significance in the realm of industrial automation, offering a plethora of advantages. By exploring six key aspects of PRCs, we can gain a deeper understanding of their capabilities and impact.
- Programmability: PRCs can be tailored to specific automation requirements.
- Networking: They seamlessly integrate with distributed systems, enabling remote monitoring and control.
- Reliability: PRCs ensure continuous operation, minimizing downtime.
- Data acquisition: They collect and process data from sensors for comprehensive analysis.
- Control: PRCs precisely control actuators based on sensor inputs and programmed logic.
- Compactness: Their compact design allows for easy installation in space-constrained environments.
These aspects collectively highlight the versatility and effectiveness of PRCs. For instance, their programmability empowers users to adapt them to unique automation needs, while their networking capabilities facilitate remote troubleshooting and maintenance. Moreover, the reliability of PRCs ensures uninterrupted operation, increasing productivity and reducing downtime. Overall, PRCs are indispensable components in modern industrial automation systems.
Programmability
The programmability of programmable rednet controllers (PRCs) sets them apart as versatile tools in industrial automation. This feature allows users to customize the behavior of PRCs to meet the specific needs of their applications.
- Customizable Logic: PRCs can be programmed with custom logic to automate complex processes. This eliminates the need for hardwired controllers, providing greater flexibility and adaptability.
- Flexible Configuration: The programmability of PRCs allows users to easily reconfigure them for different tasks. This reduces downtime and costs associated with hardware changes.
- Integration with External Systems: PRCs can be programmed to communicate with other systems, such as PLCs, SCADA systems, and databases. This enables seamless integration and data exchange.
- Remote Updates: The ability to remotely update the program of a PRC allows for quick and efficient deployment of bug fixes and new features.
In summary, the programmability of PRCs empowers users to create tailored automation solutions that meet the unique requirements of their applications. This flexibility and adaptability make PRCs a valuable asset in modern industrial automation systems.
Networking
The networking capabilities of programmable rednet controllers (PRCs) are a cornerstone of their value in industrial automation. By seamlessly integrating with distributed systems, PRCs empower users with remote monitoring and control, unlocking a range of benefits.
The ability to remotely monitor and control processes and machinery offers significant advantages. For instance, in manufacturing settings, PRCs can be used to monitor production lines remotely, enabling early detection of potential issues and minimizing downtime. Additionally, PRCs allow for remote control of equipment, reducing the need for on-site personnel and increasing operational efficiency.
The networking capabilities of PRCs also facilitate the creation of distributed control systems. In such systems, multiple PRCs can be interconnected to coordinate and control complex processes across different geographical locations. This enables centralized monitoring and management, reducing operational costs and improving overall system reliability.
In summary, the networking capabilities of PRCs are essential for realizing the full potential of industrial automation. They enable remote monitoring and control, facilitate the creation of distributed control systems, and ultimately enhance productivity, efficiency, and safety in industrial environments.
Reliability
Reliability is a crucial aspect of programmable rednet controllers (PRCs) in industrial automation. PRCs are designed to ensure continuous operation, minimizing downtime and maximizing productivity. Several key factors contribute to the reliability of PRCs:
- Robust Hardware: PRCs are typically built with industrial-grade hardware components, ensuring they can withstand harsh environmental conditions, vibrations, and electrical noise.
- Redundancy: PRCs can be configured with redundant components, such as dual power supplies and communication modules. If one component fails, the backup takes over seamlessly, preventing system downtime.
- Error Detection and Correction: PRCs employ sophisticated error detection and correction mechanisms to identify and rectify errors in data transmission and processing.
- Predictive Maintenance: PRCs can monitor their own health and performance, providing early warnings of potential issues. This enables proactive maintenance and prevents unexpected failures.
The reliability of PRCs is essential for mission-critical industrial applications. By minimizing downtime, PRCs help maintain production schedules, reduce maintenance costs, and ensure the smooth operation of automated systems.
Data acquisition
Data acquisition is a fundamental aspect of programmable rednet controllers (PRCs) in industrial automation. PRCs are equipped with the ability to collect and process data from various sensors, providing valuable insights for process monitoring, optimization, and control.
- Real-Time Monitoring: PRCs enable real-time monitoring of sensor data, allowing operators to track key process parameters and make informed decisions. This helps identify trends, detect anomalies, and prevent potential issues.
- Predictive Maintenance: By analyzing sensor data, PRCs can predict the health and performance of equipment. This enables proactive maintenance, preventing unexpected failures and minimizing downtime.
- Process Optimization: PRCs can use sensor data to optimize process parameters, such as temperature, pressure, and flow rates. This helps improve product quality, reduce energy consumption, and maximize production efficiency.
- Remote Diagnostics: PRCs allow for remote access to sensor data, enabling experts to diagnose issues and provide support from anywhere. This reduces troubleshooting time and minimizes production disruptions.
In summary, the data acquisition capabilities of PRCs are essential for comprehensive process monitoring, optimization, and control. By collecting and processing sensor data, PRCs provide valuable insights that help improve productivity, efficiency, and reliability in industrial automation systems.
Control
The control capabilities of programmable rednet controllers (PRCs) are a fundamental aspect of their functionality in industrial automation systems. PRCs use sensor inputs and programmed logic to precisely control actuators, enabling automated and efficient operation of machinery and processes.
- Real-Time Control: PRCs perform real-time control by continuously monitoring sensor inputs and adjusting actuator outputs accordingly. This ensures precise control over process parameters, such as temperature, pressure, and flow rates.
- Complex Logic: PRCs can be programmed with complex logic to handle a wide range of control scenarios. This allows them to perform advanced operations, such as PID control, motion control, and sequencing.
- Feedback Mechanisms: PRCs utilize feedback mechanisms to maintain desired setpoints. By comparing sensor readings to target values, PRCs adjust actuator outputs to minimize errors and achieve stable operation.
- Remote Control: PRCs can be remotely controlled and monitored, allowing operators to make adjustments and troubleshoot issues from anywhere. This enhances operational flexibility and reduces downtime.
The control capabilities of PRCs provide several benefits in industrial automation. They improve process efficiency, reduce production costs, and enhance safety by ensuring precise and reliable control of machinery and systems.
Compactness
The compactness of programmable rednet controllers (PRCs) is a critical factor in their widespread adoption in industrial automation. Their small size and modular design make them suitable for installation in space-constrained environments, offering several advantages:
- Optimized Space Utilization: The compact form factor of PRCs enables efficient use of space in control cabinets and on production lines. This is particularly advantageous in industries with limited floor space, such as manufacturing and energy.
- Simplified Installation: The compact size and lightweight nature of PRCs simplify their installation and maintenance. They can be easily mounted on walls, panels, or DIN rails, reducing installation time and costs.
- Portability and Flexibility: The compact design makes PRCs highly portable and flexible. They can be easily moved and redeployed to different locations or applications, providing versatility in automation systems.
- Cost-Effective Integration: The small size of PRCs reduces the need for additional enclosures or mounting systems, leading to cost savings in installation and maintenance.
In summary, the compactness of programmable rednet controllers empowers industries to maximize space utilization, simplify installation, enhance flexibility, and optimize costs. These advantages make PRCs a valuable asset in space-constrained industrial environments.
FAQs on Programmable Rednet Controllers
This section addresses frequently asked questions (FAQs) regarding programmable rednet controllers (PRCs), providing concise and informative answers to clarify common concerns and misconceptions.
Question 1: What are the primary applications of PRCs in industrial automation?
PRCs are versatile devices widely used in industrial automation for various applications, including process control, monitoring, data acquisition, and remote management of machinery and systems.
Question 2: How do PRCs contribute to improved efficiency in industrial processes?
PRCs enhance efficiency by automating tasks, optimizing process parameters, and providing real-time monitoring capabilities. This leads to increased productivity, reduced downtime, and improved resource utilization.
Question 3: Are PRCs suitable for use in harsh industrial environments?
Yes, PRCs are typically designed to withstand harsh industrial conditions. They are built with robust hardware components and employ protective measures to ensure reliable operation in environments with extreme temperatures, vibrations, and electrical noise.
Question 4: How does the networking capability of PRCs benefit industrial automation systems?
Networking capabilities allow PRCs to communicate with other devices and systems over a network. This enables remote monitoring, control, and data exchange, facilitating centralized management and improving overall system integration.
Question 5: What are the key factors to consider when selecting a PRC for a specific industrial application?
When selecting a PRC, important factors to consider include the number of I/O points required, communication protocols supported, processing power, memory capacity, and the specific features and functionality needed for the intended application.
Question 6: How can PRCs contribute to sustainability in industrial operations?
PRCs play a role in sustainability by enabling efficient energy management, optimizing resource utilization, and reducing waste. They can monitor and control energy consumption, adjust processes based on real-time data, and implement predictive maintenance strategies to minimize downtime and extend equipment life.
In summary, PRCs offer numerous benefits in industrial automation, enhancing efficiency, reliability, and flexibility. Their versatility and adaptability make them suitable for diverse applications, contributing to improved productivity, reduced costs, and increased sustainability in industrial operations.
Tips on Utilizing Programmable Rednet Controllers
Programmable rednet controllers (PRCs) offer a comprehensive solution for industrial automation, providing numerous benefits and enhancing operational efficiency. To maximize the effectiveness of PRCs, consider the following tips:
Tip 1: Define Clear Objectives and RequirementsA well-defined set of objectives and requirements is crucial before implementing PRCs. Determine the specific tasks to be automated, the desired outcomes, and the necessary features and capabilities of the PRC. This will ensure that the selected PRC aligns precisely with the intended application.Tip 2: Choose the Right PRC for Your ApplicationSelecting the appropriate PRC involves evaluating factors such as the number of input/output (I/O) points required, communication protocols supported, processing power, memory capacity, and specialized features. Consider the specific needs of the application and choose a PRC that meets or exceeds those requirements.Tip 3: Plan for Scalability and Future ExpansionConsider the potential for future expansion and scalability when selecting a PRC. Choose a device that can accommodate additional I/O modules or expansion boards to meet growing automation needs. This foresight will prevent the need for costly replacements or redesigns in the future.Tip 4: Utilize Networking CapabilitiesPRCs with networking capabilities offer remote access, monitoring, and control. Leverage this feature to enable centralized management, data acquisition from remote locations, and quick troubleshooting. Networking also facilitates integration with other systems and devices within the industrial environment.Tip 5: Implement Robust Security MeasuresProtecting PRCs and the automated systems they control from unauthorized access and cyber threats is essential. Implement robust security measures such as password protection, encryption, and network segmentation to safeguard sensitive data and maintain operational integrity.Tip 6: Prioritize Preventative MaintenanceRegular maintenance is crucial to ensure the longevity and reliability of PRCs. Establish a preventive maintenance schedule that includes periodic inspections, firmware updates, and cleaning. This proactive approach minimizes the risk of unexpected failures and downtime.Tip 7: Train Personnel on PRC Operation and MaintenanceProper training of personnel responsible for operating and maintaining PRCs is essential. Ensure that they have a thorough understanding of the PRC’s functionality, programming, and safety protocols. This investment in training empowers personnel to maximize the PRC’s capabilities and minimize operational disruptions.Tip 8: Leverage Technical Support and ResourcesMany PRC manufacturers and suppliers offer technical support and resources to assist users. Utilize these resources to access documentation, troubleshooting guides, and expert advice. This support can be invaluable in resolving issues quickly and efficiently, minimizing downtime and maximizing productivity.
By following these tips, you can effectively utilize programmable rednet controllers to enhance your industrial automation processes, improve efficiency, and achieve your desired outcomes.
Conclusion
Programmable rednet controllers (PRCs) stand as versatile and powerful tools in the realm of industrial automation. They offer a comprehensive solution for automating tasks, optimizing processes, and enhancing operational efficiency. PRCs seamlessly integrate with distributed systems, providing remote monitoring and control capabilities, while their compact design allows for easy installation in space-constrained environments.
The adoption of PRCs has revolutionized industrial automation, facilitating the development of smart factories and Industry 4.0 initiatives. Their ability to collect and process data from sensors enables comprehensive analysis and predictive maintenance, leading to increased productivity and reduced downtime. Moreover, the programmability of PRCs empowers users to tailor them to specific automation requirements, ensuring a perfect fit for diverse applications.
Youtube Video:
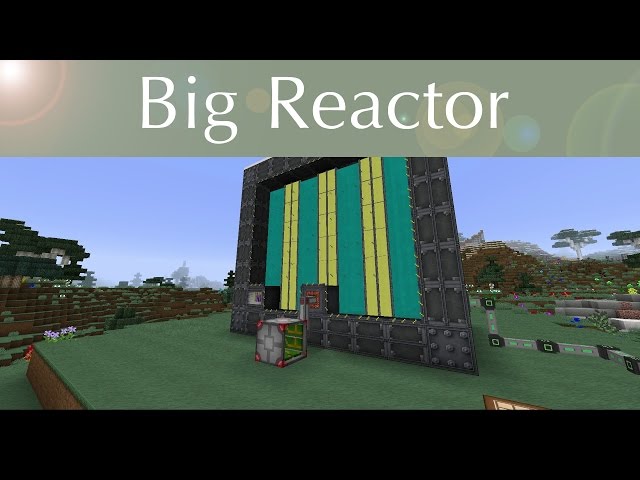
Tags: controller, programmable, rednet